A ceramic renaissance

Chao Ma, an associate professor of manufacturing engineering in ASU's Ira A. Fulton Schools of Engineering, researches binder jet additive manufacturing, a versatile 3D-printing technique. Ma’s work is supported by the National Science Foundation Faculty Early Career Development Program (CAREER) award. Photo courtesy of Chao Ma
Rising from the smoky embrace of kilns, ceramics played a significant role during the Renaissance era, with the resurgence of sculptors who originally used the material as a form of classical artistic expression.
Today, ceramics are essential for household use and scientific applications, serving as catalysts for creating new materials in the environmental, chemical and energy sectors.
Chao Ma, an associate professor of manufacturing engineering in the Ira A. Fulton Schools of Engineering at Arizona State University, says this versatile class of materials now has a place in advanced industrial settings.
Although conventional ceramic manufacturing processes pose challenges including structural limitations, prolonged production timelines and high costs, binder jet additive manufacturing — or BJAM — offers a solution that enhances manufacturing capabilities.
“The largest barrier so far has been the lack of fundamental research on ceramic BJAM,” Ma says.
To advance ceramic BJAM, Ma — a faculty member in the School of Manufacturing Systems and Networks, part of the Fulton Schools — earned a National Science Foundation Faculty Early Career Development Program (CAREER) award. The CAREER award supports faculty members with the potential to become academic role models excelling in research and education.
With the $600,000 CAREER project funding, Ma is exploring a new technique to regulate the density of BJAM-produced objects across a broad spectrum to improve the material’s quality.
“BJAM will allow the production of ceramic products in almost any shape,” Ma says. “This geometric flexibility will make it possible to manufacture products customized for use with higher quality.”
BJAM offers additional advantages such as high speed, low cost and the ability to produce functional parts out of almost any material. Industries such as aerospace, health care, energy and tooling can particularly benefit from this innovative additive manufacturing technique.
BJAM is a 3D-printing technology utilizing a layer-by-layer approach to construct objects.
To initiate the build process, a fine layer of a powdered substance is evenly distributed across the build box, where a roller moves back and forth to spread and gently compact the fresh powder layer.
Next, a liquid binding agent is deposited onto the powder bed, causing the particles to combine and form a solid layer.
This process repeats, with each layer of powder receiving the binding agent until the object is complete as per its original design specifications.
Exploration into this technique could unveil a complex relationship between certain parameters and the resulting material structure, encouraging further research into ceramic manufacturing.
“My approach combines a tailored feedstock powder and an emerging powder-bed formation method to control the density,” Ma says.
This control is essential for achieving the desired structural integrity, functional properties and overall performance of the final product.
Ma says he believes granule characteristics affect compaction behaviors, enabling the density control of ceramic parts.
Granules are assemblies of smaller particles used as the feedstock material for BJAM. The granules vary in structure, density and strength, determining the quality and performance of BJAM-manufactured products.
After unlocking new density-control capabilities, Ma envisions various applications for BJAM.
“One of the applications I am pursuing is direct air capture of carbon dioxide using sorbents produced by ceramic binder jet additive manufacturing,” he says. “It will help lower the carbon dioxide concentration in the air and reduce the frequency and intensity of natural disasters caused by global warming.”
More Science and technology

Stuck at the airport and we love it #not
Airports don’t bring out the best in people.Ten years ago, Ashwin Rajadesingan was traveling and had that thought. Today, he is an assistant professor at the University of Texas at Austin, but back…

ASU in position to accelerate collaboration between space, semiconductor industries
More than 200 academic, business and government leaders in the space industry converged in Tempe March 19–20 for the third annual Arizona Space Summit, a statewide effort designed to elevate…
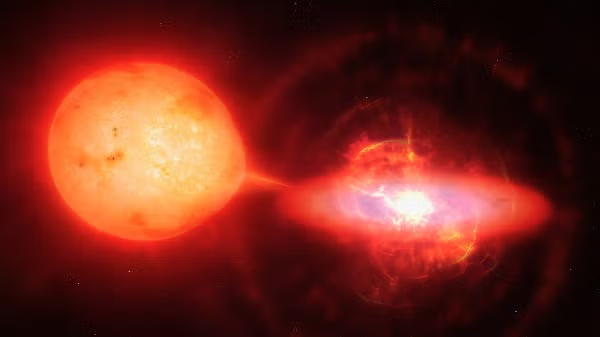
A spectacular celestial event: Nova explosion in Northern Crown constellation expected within 18 months
Within the next year to 18 months, stargazers around the world will witness a dazzling celestial event as a “new” star appears in the constellation Corona Borealis, also known as the Northern Crown.…