ASU students beat the heat with 3D-printed thermal tech
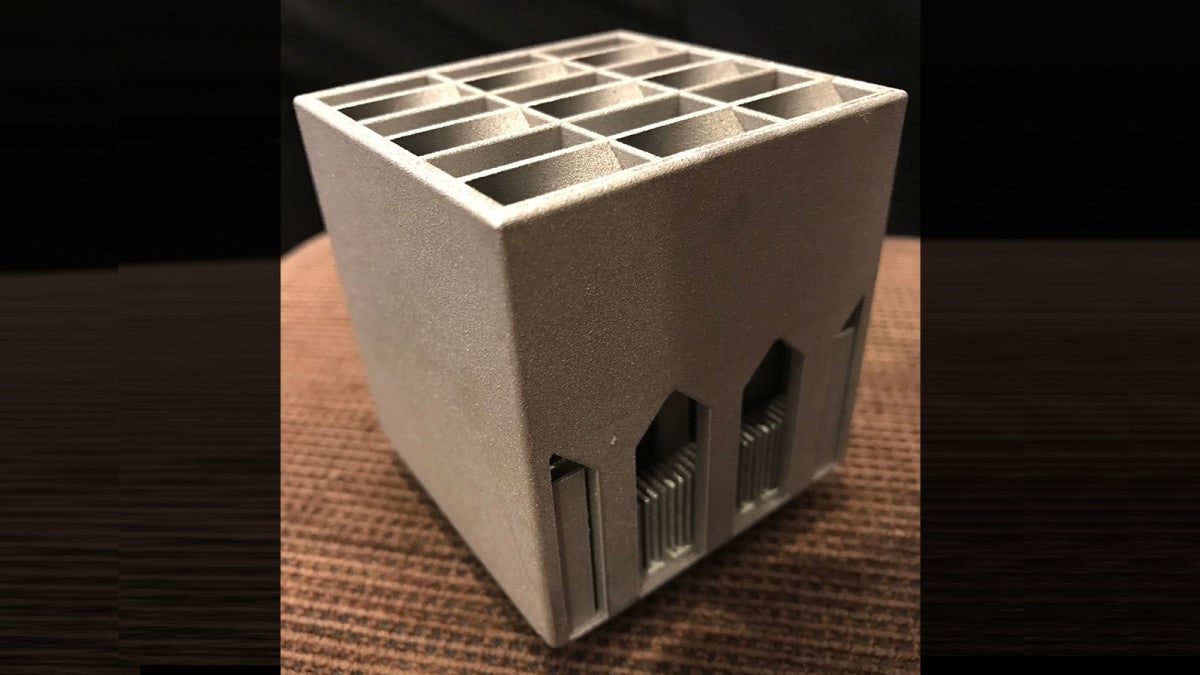
The 3D-printed aluminum heat sink was designed by ASU students Faizan Ejaz, Munku Kang and Gokul Chandrasekaran. Photo courtesy of Beomjin Kwon
Heat sinks, used to regulate the temperature of electronic devices, are more pertinent now than ever, especially with the increased demand for personal devices such as laptop computers.
Without the cooling provided by heat sinks, electrical components would overheat and these types of devices would see significantly decreased longevity. Heat-sink manufacturing technology hasn’t changed much over time, but metal 3D printing could change that.
The 18th Intersociety Conference on Thermal and Thermomechanical Phenomena in Electronic Systems challenged students to find innovative ways to take advantage of modern-day manufacturing technologies to design heat sinks in a new way.
The conference, which invited industry leaders along with university students and faculty to network and discuss advances in heat-transfer technology, hosted a student heat-sink design competition mainly sponsored by General Electric. A team of students from the Ira A. Fulton Schools of Engineering at Arizona State University placed among the top five finalists out of 21 teams worldwide.
Instead of designing the heat sink to be manufactured traditionally using casting, metal extrusion and other similar technologies, students were tasked with designing a heat sink using metal 3D-printing technology. This process of manufacturing in which objects are built layer-by-layer is referred to as additive manufacturing.
The ASU team consisted of three mechanical engineering doctoral students — Faizan Ejaz, Munku Kang and Gokul Chandrasekaran — under the guidance of Assistant Professor Beomjin Kwon. Their design utilized 3D-printing technology to create designs that would otherwise be impossible to manufacture.
“There are some features that you cannot make with conventional methods,” Ejaz said. “If you want to make a cylindrical honeycomb structure, you cannot manufacture it without requiring other expensive postprocessing steps. … With the advent of additive manufacturing, now we have access to manufacturing very complex geometries.”
Additive manufacturing allows engineers to create more complex designs, providing a larger surface area on the heat sink. This allows for more hot air from the electrical components to flow across the heat sink without necessarily compromising its efficiency, a design restriction prevalent in traditional manufacturing.
“In many cases, we have to compromise between the manufacturing constraints and the device performance,” Kwon said. “So in real experiments, we do not have a truly optimized device. But additive manufacturing now eliminates many design constraints imposed by traditional techniques. We can think about further optimized design compared to traditional heat-transfer devices.”
The team used concepts from their engineering classes to come up with ways to make the most of their newfound design freedom and maximize efficiency, eventually settling on a design that swirled the air as it flowed, promoting better air mixing and inducing turbulence, which led to enhanced heat transfer.
In addition to applying classroom concepts in a real-world scenario, the team had the opportunity to work in uncharted territory for heat-sink manufacturing and acquire skills in creative design.
“The design freedom you get while applying additive manufacturing techniques is immense,” Chandrasekaran said. “The competition was more about providing innovative solutions to the problem than applying the traditional approach we already know.”
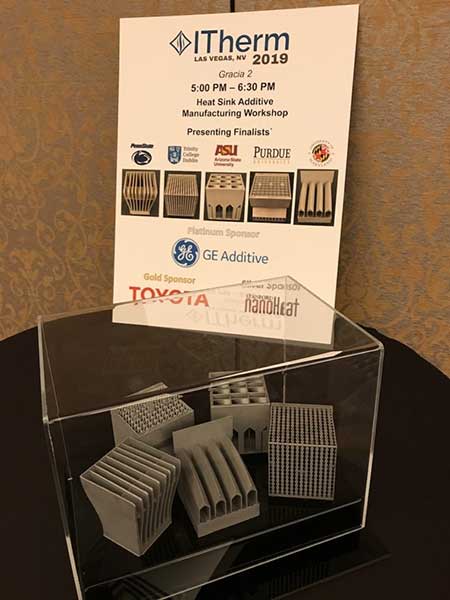
The top five finalists of the heat-sink design competition presented their designs at the IEEE ITherm conference in Las Vegas. Photo courtesy of Beomjin Kwon
The other finalists included teams from Purdue University, the University of Maryland, Trinity College Dublin and Pennsylvania State University.
“Everybody got to see our designs,” Ejaz said. “All five designs of the top teams were incredible, and each one had its own unique design style and unique approach to the problem, so we got to learn a lot about different ideas and how to think better.”
The competition also gave students the opportunity to work directly with industry leaders from GE and receive feedback and guidance on their designs.
GE set up video conferences with students who made it past the first round of the competition and assisted them in designing their heat sinks. Once the final designs were submitted, GE 3D-printed the heat sinks with aluminum and tested them. The top five finalists received admission to the conference and presented their designs.
“The competition helps you to explore your design capabilities and your potential to work in a team,” Ejaz said. “But the best thing about this competition is that you are working directly with GE and they are helping you to become leaders in metal 3D manufacturing.”
The ASU team’s accomplishments open up new opportunities for future research at the university using smart technologies such as machine learning to optimize designs.
“In this competition, we came up with a design from our intuition and based on our experience, and based on student effort,” Kwon said. “But I think the future work will be about how to produce the device's design in a smart way, in a more systematic way.”
More Science and technology

ASU professor honored with prestigious award for being a cybersecurity trailblazer
At first, he thought it was a drill.On Sept. 11, 2001, Gail-Joon Ahn sat in a conference room in Fort Meade, Maryland.…

Training stellar students to secure semiconductors
In the wetlands of King’s Bay, Georgia, the sail of a nuclear-powered Trident II Submarine laden with sophisticated computer…
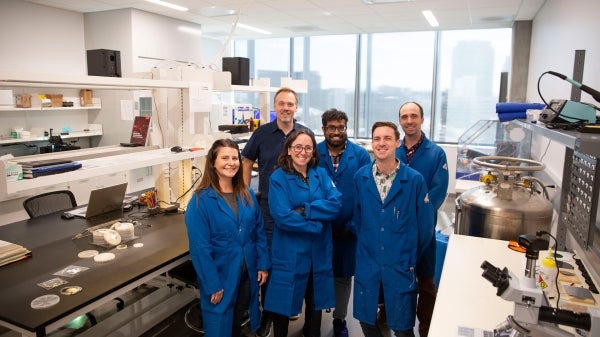
ASU startup Crystal Sonic wins Natcast pitch competition
Crystal Sonic, an Arizona State University startup, won first place and $25,000 at the 2024 Natcast Startup Pitch Competition at…