Curtailing unhealthy impacts of steel production

Iron making, coking, smelting of ores and other processes involved in the manufacture of steel are among sources of air, water and soil pollution and other contaminating processes and substances. Faculty members in the Ira A. Fulton Schools of Engineering at ASU are joining colleagues in a range of related engineering and science fields at research universities in Texas and New Mexico and a national laboratory to contribute to overcoming challenges of the drawbacks of the country’s ever-expanding reliance on steel. Photo courtesy iStock
Emissions from millions of automobiles powered by fossil fuels continue to pose a serious threat to the Earth’s environmental health. But they’re not alone in doing such damage.
Many industrial processes are exacerbating the problem by putting substances into the atmosphere and endangering the well-being of people and nature.
One prevalent source of such negative consequences is the manufacturing of one of the world’s most useful and valuable materials: steel.
Making steel is among the most carbon-intensive manufacturing processes, producing about 7% of carbon dioxide emissions globally. Steel production is part of a broader industrial sector that accounted for about 30% of the greenhouse gas emissions in the U.S. in 2021, according to the Environmental Protection Agency.
Those emissions trap heat from the sun, which causes global warming, leading to climate changes that are altering weather patterns and disrupting natural environmental processes.
“The disruption is a growing threat that is going to require a combination of research breakthroughs and technological innovations to stop,” says Professor Sridhar Seetharaman, chief science officer in the School for Engineering of Matter, Transport and Energy, part of the Ira A. Fulton Schools of Engineering at Arizona State University.
Declaring need for decarbonization
To help solve the problem, ASU was selected earlier this year by the U.S. Department of Energy, or DOE, to help establish a clean energy manufacturing institute to take on the challenges of curbing greenhouse gas emissions resulting from industrial process heating, a large source of carbon emissions from the use of fossil fuels.
As part of the project, ASU now leads the Electrified Processes for Industry without Carbon, or EPIXC, a multi-institution effort directed by Seetharaman.
EPIXC joins the DOE’s six other Manufacturing USA institutes, which are working to move new clean electrification processes out of the lab and into the marketplace.
The goals of EPIXC include eliminating carbon emissions by developing the technologies and workforce required to replace fossil fuel-based heating with electric power sources, as well as significant decarbonization of industrial processes using clean energy sources.
RELATED: ASU to lead new DOE Clean Energy Manufacturing Innovation Institute
The efforts emanate from the DOE’s climate and economic competitiveness aspirations related to two programs. The Office of Energy Efficiency and Renewable Energy Industrial Heat Shot program, part of an Energy Earthshots Initiative, seeks to develop cost-competitive industrial heat decarbonization technologies that drastically lower greenhouse gas emissions. The DOE office’s Clean Fuels and Products Shot aims to decarbonize the fuel and chemical industry through solutions for sectors in which it is difficult to eliminate carbon, such as aircraft and marine fuels.
The research led by Seetharaman to be conducted through the Basic Energy Sciences program within the DOE’s Office of Science is formally titled “Fundamental studies of hydrogen arc plasmas for high-efficiency and carbon-free steelmaking.”
Eco-friendly production
The research team will develop a hydrogen-plasma-smelting-reduction technology to dramatically reduce carbon emissions during the steelmaking process.
The project will involve a collaboration between Seetharaman, three other Fulton Schools faculty members, and eight researchers at the University of Texas at Austin, Navajo Technical University in New Mexico and the National Renewable Energy Laboratory in Colorado.
The team’s big challenge? Finding a clean, energy-efficient way to make steel with fewer impurities.
It’s possible to use hydrogen to replace carbon-emitting sources or to use ore to produce iron for steelmaking without emitting carbon dioxide. However, the existing technologies for these processes produce solid iron containing impurities, called “gangue,” which can render steel useless for many applications by damaging its structural integrity.
It’s difficult to remove impurities with electric arc furnaces used by most U.S. steel mills, but an alternative process using hydrogen in a plasma state would provide a molten iron separated from the impurities.
Hydrogen plasma smelting reduction of iron ore is only a concept at this point, according to the team’s project description. However, it is a promising tool to develop for dramatically reducing carbon emissions from steel production while expanding the variety of usable iron ore.
Seetharaman says he foresees the scientific insights and theories arising from the project enabling steel makers to design and develop both technically and economically viable plasma reactors to enable carbon-free steelmaking.
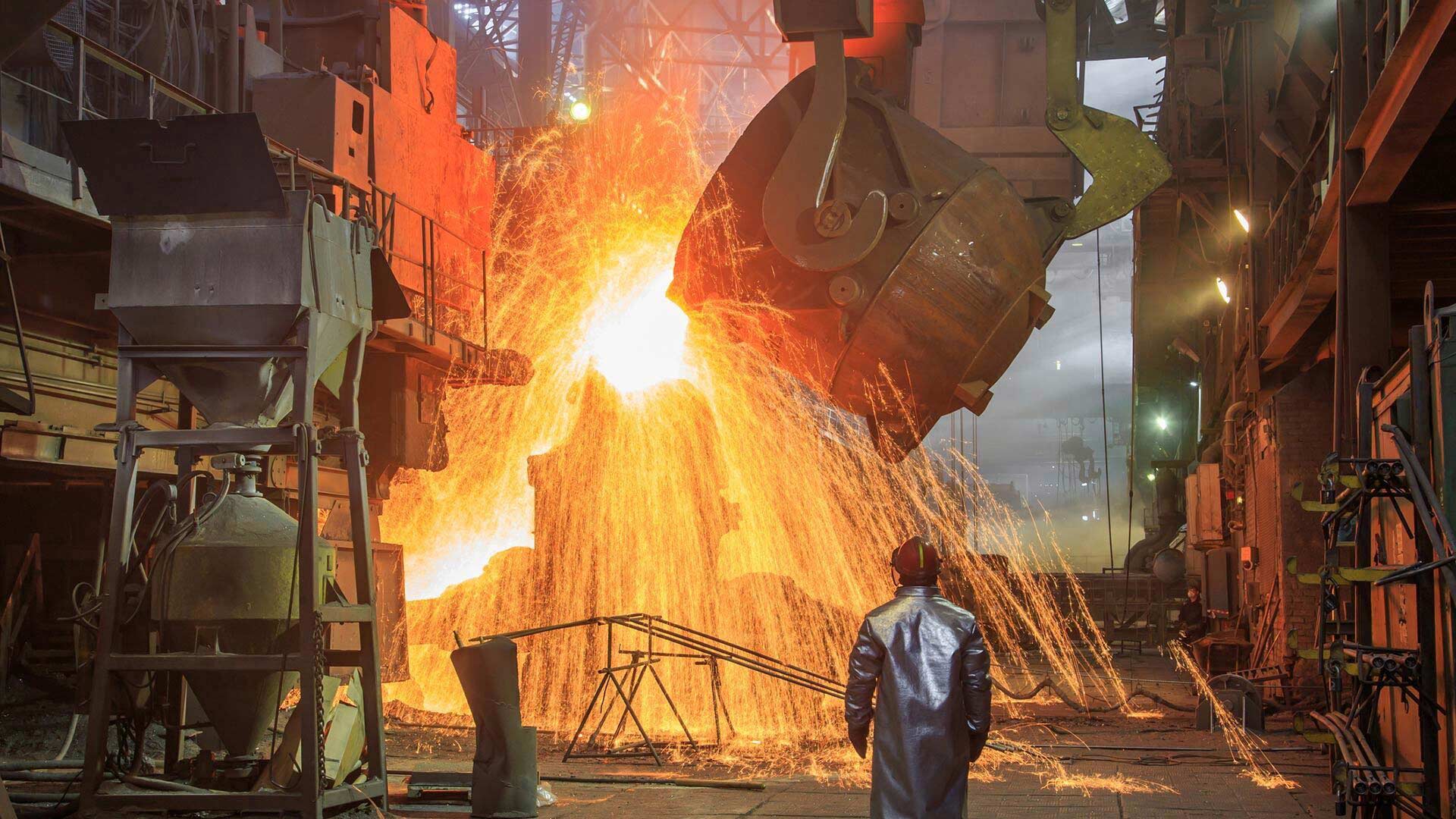
The fiery molten metals used in the making of steel emit electromagnetic, infrared and ultraviolet radiation during the manufacturing process, which can present potentially serious hazards to workers’ health and to the safety of the surrounding environment. Arizona State University engineering researchers are advancing the electrification of steel manufacturing to help to reduce or alleviate such threats. Photo courtesy iStock
Plethora of societal benefits
Three faculty members in the School for Engineering of Matter, Transport and Energy, part of the Fulton Schools, involved in the project are looking forward to their work contributing to multiple valuable advances.
“My piece of this puzzle is to understand the atomistic behavior of the reduction reactions," says Christopher Muhich, an assistant professor of chemical engineering. “We will use density functional theory to really understand how iron oxides, the raw material that goes into steel, turn into metal.”
Muhich says his research will focus on fine-tuning the fundamentals of iron and oxygen ion diffusion and the related chemistry required to formulate models of the process for optimal steelmaking.
Kumar Ankit, an associate professor of materials science and engineering, will use advanced computer simulations to determine how to make steel without emitting carbon dioxide. His group will use the simulations to understand different parts of the steelmaking process and to create a detailed computer model to understand how impurities can be removed from liquid metal.
“This innovation not only benefits the environment by mitigating climate change but also demonstrates the potential for cutting-edge computational and machine learning techniques to transform industrial processes, making it valuable for both the scientific community and society as a whole,” Ankit says.
Qijun Hong, an assistant professor of materials science and engineering, says the importance of this work is immeasurable because of its potential to dramatically reduce industrial carbon emissions to help mitigate climate change.
“My contribution revolves around utilizing computational methods to investigate the melting of iron ore and its properties in a liquid state,” Hong says. “Modeling liquids poses considerably more challenges compared to solids. But it aligns perfectly with my group’s expertise, and we are committed to advancing our capabilities to study such a crucial system.”
Seetharaman adds, “Ultimately, we will produce comprehensive models and simulations based on our research to show how proposed solutions will work. That will help give the DOE and others what is needed to predict the effectiveness of various options and their economic feasibility.”
More Science and technology

Science meets play: ASU researcher makes developmental science hands-on for families
On a Friday morning at the Edna Vihel Arts Center in Tempe, toddlers dip paint brushes into bright colors, decorating paper…

ASU water polo player defends the goal — and our data
Marie Rudasics is the last line of defense.Six players advance across the pool with a single objective in mind: making sure that…

Diagnosing data corruption
You are in your doctor’s office for your annual physical and you notice the change. This year, your doctor no longer has your…