In the weeks leading up to the start of the fall 2020 semester, Arizona State University was busy preparing its classrooms, installing equipment for the new ASU Sync experience. But because of a parts shortage due to the pandemic, ASU’s timeline was almost jeopardized, leading the university to do what it does best: find an innovative solution.
Like many families looking for in-demand products during this pandemic (think disinfecting wipes and toilet paper), colleges and universities across the country were ordering camera mounts to get classrooms ready for virtual instruction. As a result, the University Technology Office was short 60 mounts, and the manufacturer working with ASU wasn’t able to deliver before Aug. 20 — the first day of classes. Once the word got out that UTO needed help, ASU’s Instrument Design and Fabrication Core Facility offered to manufacture the parts in-house on the Tempe campus.
IDF, which is part of ASU’s Core Research Facilities, was established in 2016 and is at the forefront of innovation. This is the place where dream projects come to life — built by expert staff with advanced mechanical assembly design and prototyping skills. The facility specializes in electronics, glassblowing and machining; it has a self-service machine shop.
Led by Director Brian Ipema, the IDF team supports a variety of projects universitywide and for peer universities and private industry partners. Because of its capabilities, this highly specialized research facility was able to order materials, cut, weld, paint and assemble 20 camera mounts within 10 days of UTO’s initial inquiry. Eight days later, the team made 40 more.
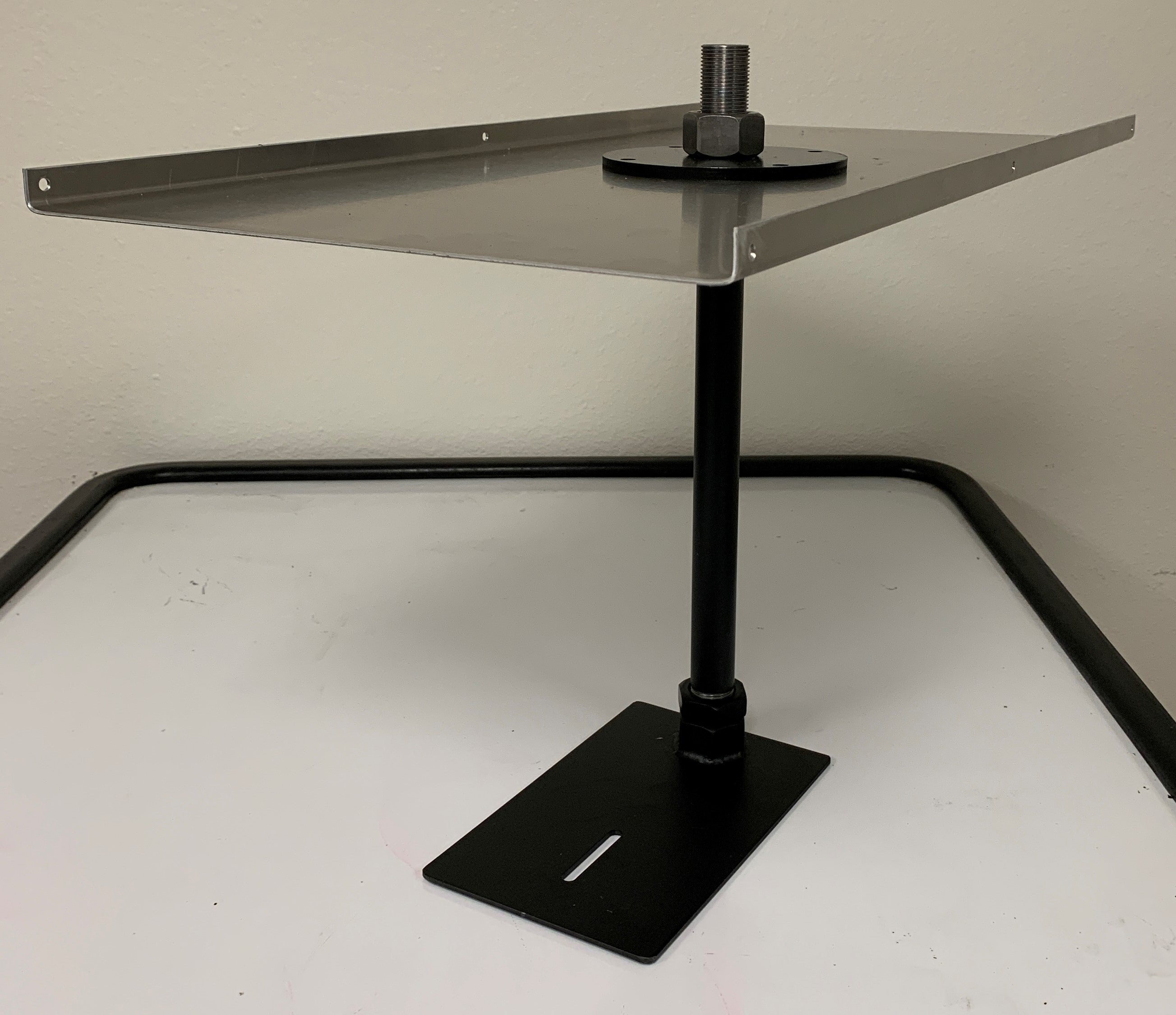
ASU's Instrument Design and Fabrication Core Facility made dozens of camera mounts for the University Technology Office after a parts shortage during ASU Sync installation. Photo credit: ASU
“The fact that we exhausted every external avenue for getting the camera mounts we needed in time for the fall semester is a great example of how tricky COVID-19 is to work around, especially as it concerns any equipment that could be used for distance/synchronous learning and remote work,” said Corey Marshall, manager of learning space technology design and integration. “If not for Brian and team, we’d have had to completely rethink a large piece of the ASU Sync strategy.”
The versatile design was carefully chosen so it could be used in various buildings, depending on the structure’s age and materials. Marshall added that his team was “bowled over,” explaining the mounts looked identical to the example provided to IDF.
“There are a lot of people involved in this, and we’re just one small part of it,” said Ipema. “We just happen to be fortunate enough that we have the capabilities here to be flexible, to move over to a direction to try and assist in supporting what is needed right now.”
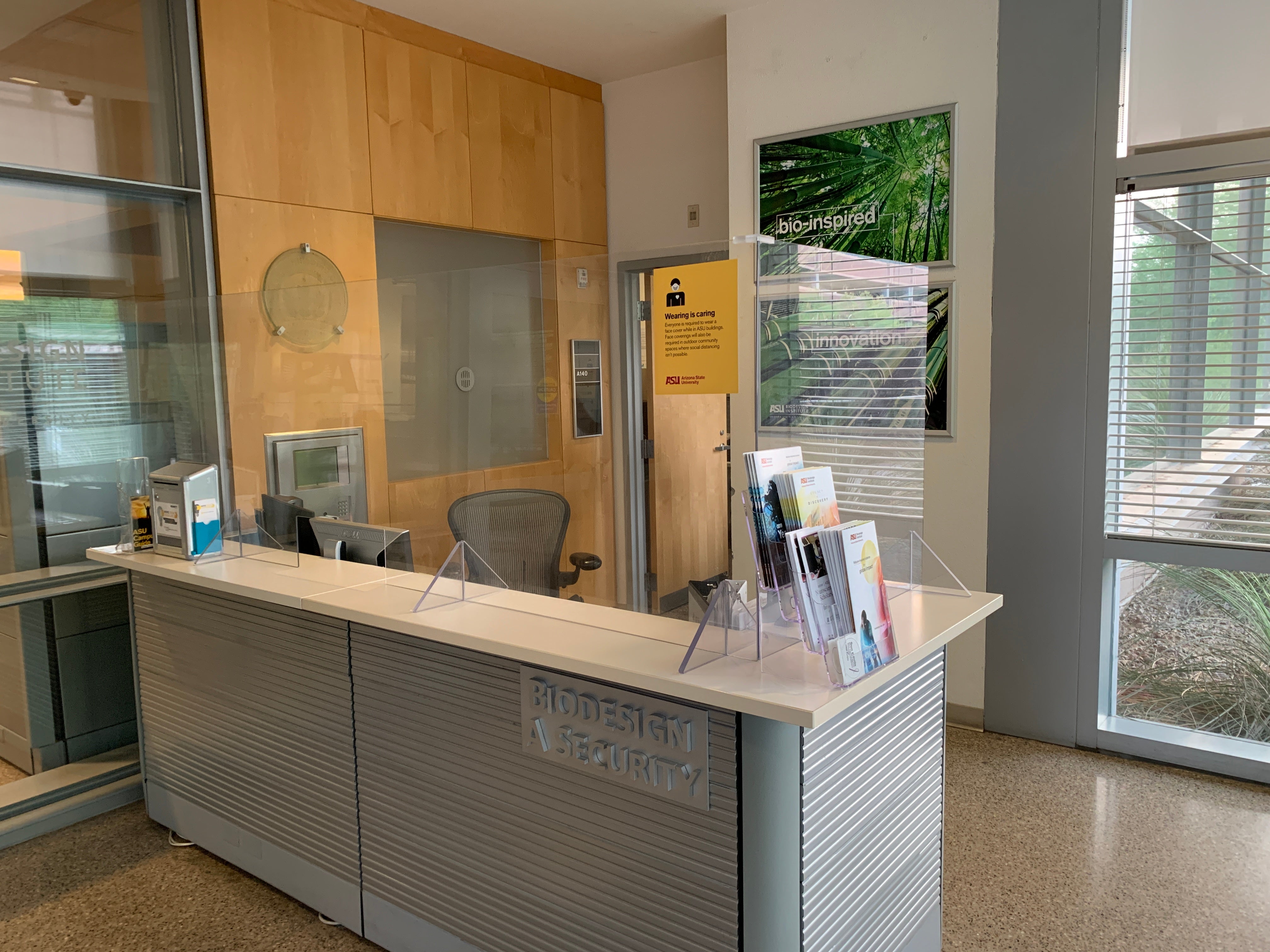
The Instrument Design and Fabrication Core Facility installed clear safety shields in various ASU buildings, including Biodesign Institute Building A. Photo credit: ASU
This isn’t the first time IDF has assisted with campus projects during the pandemic. When ASU’s Biodesign Institute first introduced its saliva-based COVID-19 testing, IDF designed and manufactured free-standing, mobile test cells that protected both test subjects and sample collectors. IDF also assisted with the installation of clear safety shields in Biodesign Buildings A, B and C — along with multiple areas at ASU Skysong. Once testing ramped up and more samples needed to be processed, IDF made several dozen racks (each holds 50) to organize the test tubes, illustrating a level of detail that makes the team’s work very important. Ipema adds, “It’s the little things that are right there in front of you, but you don’t always see them.”
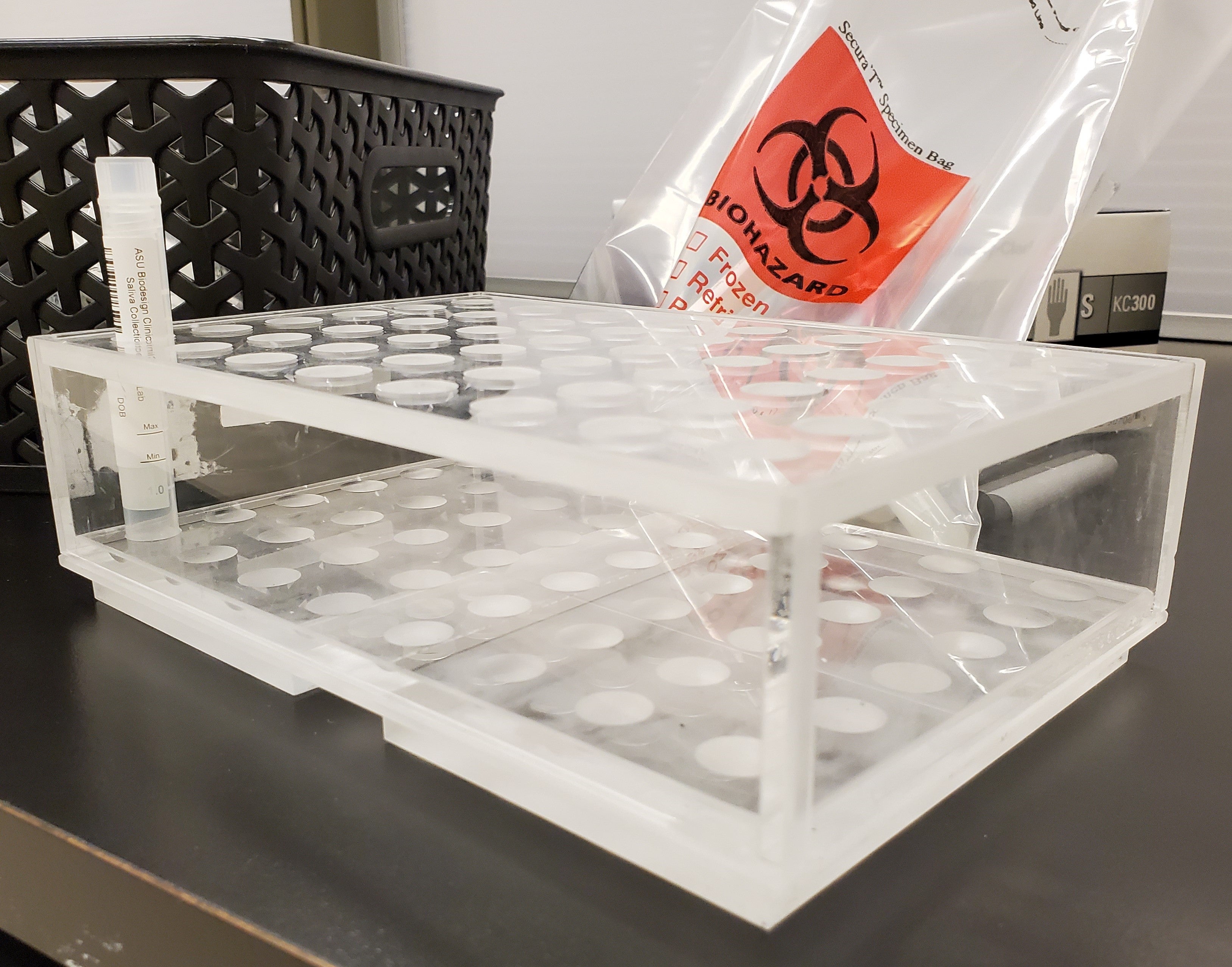
ASU's Instrument Design and Fabrication Core Facility assisted the Biodesign Institute by making dozens of tube racks for the team's COVID-19 saliva-based testing samples. Photo credit: ASU
IDF’s expertise has been critical in large ASU research projects like Biodesign’s Compact X-ray Free Electron Laser (CXFEL). For that project, IDF manufactured components to build the laser assembly. Most recently, IDF assisted with two Mars projects through the School of Earth and Space Exploration. IDF manufactured components on the Emirates Mars Infrared Spectrometer (EMIRS) aboard the Hope orbiter, and the camera mount testing fixture on Mastcam-Z aboard the Perseverance rover. Both launched in July.
The IDF team is comprised of 11 people and has been fortunate to be a part of many research projects with small-scale and global impacts — one of the many rewarding aspects of the work.
“We are always seeing something that is different, and in many cases, it’s never been done before,” said Ipema. “We’re here to assist (in the research) and to make certain that we can do as much as possible to aid in that forward movement.”
More Science and technology

ASU-led space telescope is ready to fly
The Star Planet Activity Research CubeSat, or SPARCS, a small space telescope that will monitor the flares and sunspot activity of low-mass stars, has now passed its pre-shipment review by NASA.…

ASU at the heart of the state's revitalized microelectronics industry
A stronger local economy, more reliable technology, and a future where our computers and devices do the impossible: that’s the transformation ASU is driving through its microelectronics research…

Breakthrough copper alloy achieves unprecedented high-temperature performance
A team of researchers from Arizona State University, the U.S. Army Research Laboratory, Lehigh University and Louisiana State University has developed a groundbreaking high-temperature copper alloy…