ASU students lead charge in pursuit of productivity through Department of Energy program

Other than a general interest in engineering, Ryan Milcarek’s career aspirations when he was an undergraduate lacked focus. That is until he joined the Industrial Assessment Center, or IAC, program.
“I had no idea about what I wanted to do when I started,” Milcarek said. “But the IAC just jibed for me right away. I had a fixed purpose from that point on. It was a huge turning point.”
Funded by the U.S. Department of Energy, or DOE, the IAC programs deploy teams of college students to provide primarily small to medium-sized manufacturing companies no-cost assessments of their operations to improve energy and water use efficiency, reducing resource waste and increasing productivity.
Milcarek’s two-year IAC experience at Syracuse University in New York “got (him) deep into the energy field,” which became the catalyst for efforts that earned him a scholarship and later a research fellowship. The work propelled him into graduate studies, culminating with a doctoral degree in mechanical engineering.
After completing a postdoctoral research fellowship, Milcarek landed an assistant professor position in 2018 in Arizona State University’s Ira A. Fulton Schools of Engineering.
“It all started with the IAC,” Milcarek said.
His job duties now include helping to provide similarly valuable educational and career boosts to ASU students as one of two assistant directors of the IAC program in the Fulton Schools, called IAC@ASU.
Students are getting to see what real life is like in the demanding world of competitive industries, said IAC@ASU director Rene Villalobos, an associate professor of industrial engineering in the School of Computing, Informatics, and Decision Systems Engineering, one of the six Fulton Schools.
The assessment projects “are not homework assignments,” Villalobos said. “We run things like a small business.”
He and IAC@ASU’s project manager Gamze Gungor-Demirci emphasize that while student teams are led and mentored by faculty members and ASU support staff, the students take on the roles of consultants and shoulder responsibility for completing and presenting assessments and making recommendations to the companies for improvements.
IAC@ASU Project Manager Gamze Gungor-Demirci (at left) and undergraduate engineering student Sárbith Aguilar inspect equipment at the ASU Central Heating and Power Facility. Students on IAC@ASU industrial assessment teams help companies by evaluating the effectiveness of technologies used in energy and water systems, as well as in manufacturing operations. Photo by Erika Gronek/ASU
Assessments producing long-term positive impacts on variety of industrial ventures
Students, who must apply and undergo interviews to be hired for IAC@ASU positions, are paid through DOE funding commensurate with their experience and academic status — as undergraduates, masters or doctoral students. If they satisfactorily complete at least six assessments and remain active in the program for two semesters, the students will earn an IAC certificate.
Their ultimate rewards, however, are the real-world experience and the accomplishments the students can add to their résumés.
“They often are seeing their ideas implemented and sometimes even getting involved in research projects related to the needs of companies they’ve done assessments for,” said Gungor-Demirci, an environmental engineer who has done research in many of the areas in which the program focuses.
“We are seeing some of their work having long-term impacts,” Villalobos added. “Some companies adopt ideas for better environmental practices to do important things like reducing their carbon footprint, and at the same time operating more economically.”
Students also benefit from learning to work with others in various academic disciplines and professions.
Most of the program’s participants have been students in electrical, mechanical and industrial engineering, as well as computer science and engineering management. But Villalobos and Gungor-Demirci want to recruit more students from other engineering fields and from ASU business programs. They’d even like to attract students in education and journalism.
IAC@ASU is one of 31 Industrial Assessment Centers the DOE sponsors in various regions of the United States. ASU’s program covers Arizona, western New Mexico and southern Nevada.
The IAC program was first established at ASU in 1990 and continued until 2006. The current program, started in 2016, has been renewed through 2021, and leaders are planning to apply for another renewal for an additional five years.
Since its inception, IAC@ASU has completed almost 500 energy assessments and provided more than 3,800 recommended actions, which have saved companies a cumulative total of more than $72 million in operating costs and more than 1,100 gigawatt-hours of energy — an amount roughly equivalent to what would be required to provide electricity to about 80,000 homes for a year.
About 30 students have participated since 2016. Typically, eight to 12 students are active in the program at any one time.
Companies that have implemented the student assessment teams’ recommendations over the last four years have seen an average energy cost savings of almost $43,000 annually, and an average reduction in carbon emissions from the companies’ operations of 324 tons per year.
“I don’t know of any other program that enables our students to have such an impact on our community, while at the same time aligning our educational and research efforts to solve practical problems,” said Patrick Phelan, a Fulton Schools professor of mechanical and aerospace engineering who directed IAC@ASU from 1997 to 2006 and is now one of the two assistant directors.
Students are applying what they are learning to help manufacturers seek solutions in highly specialized areas such as thermodynamics, heat transfer and fluid mechanics, smart manufacturing systems and production planning for energy and cost savings. Phelan says those are things students rarely get a chance to delve deeply into outside of long-term internships or full-time jobs.
Companies realizing significant savings on operational costs
Beyond energy and water management and cost savings, the assessment teams also often determine if there are more efficient operational models for manufacturing processes, air-conditioning and refrigeration systems, and if there are new tools and technologies that could increase companies’ overall productivity.
In a recent assessment of the Royal Paper Converting company’s commercial paper production plant in Phoenix, an IAC@ASU team identified ways energy could be saved by replacing older motors used in production operations with advanced high-efficiency models.
Changing the motors will cost the company more than $47,000, but that cost will be recouped in energy savings within 13 months.
The team also recommended upgrading to better rooftop air conditioning units, skylight installations and reducing compressed air pressure in the plant, which is expected to trim costs by more than $75,000.
Royal Paper Converting Chief Financial Officer Samir Kanuga deemed the assessment “a wonderful job,” noting that the team conducted the work in a safe and professional manner and collaborated effectively with the company’s employees.
“In the end, we received a report that helped us save a significant amount of money, which definitely exceeded my expectations,” Kanuga said.
Close to half the operations costs of a plant in Tempe operated by L3, an optical instrument manufacturer, resulted from its purchase of nitrogen gas. An IAC assessment team determined that the company could install a swing adsorption system — a gas separation technology — as a viable option to purchasing nitrogen gas. The expected result is a cost savings of more than $688,000. Additional recommendations by the team added about $120,000 to projected savings.
In another assessment, for Liberty Greenleaf, a paper converting company in Phoenix, the ASU team used industrial engineering analyses to identify an opportunity to reduce a production bottleneck, which resulted in annual savings of more than $100,000.
Christopher Gahan (in red shirt), supervisor of the ASU Central Heating and Power Facility, explains features of the plant’s operations to students and faculty members involved in IAC@ASU, one of 31 Industrial Assessment Centers around the country supported by the U.S. Department of Energy. Photo by Erika Gronek/ASU
Students are strengthening their technical and business skills
Systems engineering doctoral student Nicolas Campbell, who has been with IAC@ASU for the past two years, says the assessment projects have taught him more than much of his schoolwork over the years and have been invaluable in preparing him for an engineering career.
“I have been able to experience how various industries function, as well as learn about key equipment involved and the problems typically associated with the equipment,” Campbell said. That work has led him to get involved in electrical energy demand management research, which he was introduced to through the assessment projects.
Beyond technical and business knowledge, Campbell said students are learning important time management skills.
“One of the biggest challenges is balancing numerous tasks that all have deadlines,” he said. “At any time, we are working on reports for multiple clients, which all have strict deadlines. We also have ambitious research goals to try to meet, all while keeping up with classes.”
Miguel Peinado-Guerrero is studying for a master’s degree in industrial engineering and recently became the student leader of IAC@ASU. The program is giving him invaluable insights into the operations of multiple industries.
“We have done assessments for dairy farms, aircraft component manufacturers and many other very different companies,” Peinado-Guerrero said. “We also get a lot of opportunity to interface with local electric utilities and do energy-related research.”
He is learning how to communicate effectively with business clients, how to “fine-tune my academic knowledge” and apply it to solving real-world problems, plus developing leadership skills.
Mechanical engineering doctoral student Keshawa Bandara worked for two years as a consultant for an energy service company before going to graduate school and has since been involved in more than 30 assessments in almost three years with the IAC program.
“Every assessment has taught me something new,” Bandara said. “The IAC trained me to look at the underlying fundamental systems to find opportunities (for improvement). It is surprising to see that there is always something you can do to make a system more efficient.”
Bandara credits the program for showing students that success in engineering professions requires not only technical proficiency but administrative and management abilities, and communication and teamwork skills.
“The big benefit is seeing students succeed,” Milcarek said.
“What I love as a teacher is to see students have to deal with a really complicated problem, and to start out saying ‘I have no idea what to do,’ and then get to work and come up with a solution,” he said. “That’s as much of a real-world experience as you can get as a student.”
IAC@ASU director Villalobos wants to give more students that sense of accomplishment.
“We have continuing relationships with many of the companies we have worked with,” he said. “So, there is no shortage of opportunities for our students.”
Eight to 12 students are typically involved in the Industrial Assessment Center’s projects each semester. Current and recent members of assessment teams, along with IAC faculty and staff leaders, are pictured here on ASU’s Tempe campus. Front row (from left to right): Doctoral student Keshawa Bandara, undergraduates Sárbith Aguilar and John Romano, IAC Project Manager Gamze Gungor-Demirci, Associate Professor and IAC Director Rene Villalobos, undergraduate Derall Riley and doctoral student Jiashen Tian. Back row (from left to right): Assistant Professor and IAC Assistant Director Ryan Milcarek, doctoral students Rodrigo Ulloa Correa, Nicolas Campbell and Miguel Peinado-Guerrero, Professor and IAC Assistant Director Patrick Phelan, undergraduate Daniel Florin and Professor of Practice Abdelrahman Shuaib. Photo by Mackenzie Wodicker/ASU
Top photo: ASU engineering students Derall Riley (left), Yogeshwar Kuppa (far right) and Mackenzie Wodicker (in background) work with the Industrial Assessment Program in Arizona State University’s Ira A. Fulton Schools of Engineering, which gives students opportunities for on-the-ground experience with companies in a variety of industries. Students teams evaluate companies’ methods and processes to look for ways to improve energy and water-use efficiency and increase the overall effectiveness of manufacturing operations. Photo by Erika Gronek/ASU
More Science and technology

ASU secures NSF grant to advance data science literacy as demand soars
In an era where data permeates every facet of our lives, the importance of data literacy cannot be overstated. Recognizing this critical need, Jennifer Broatch, a professor at Arizona State…
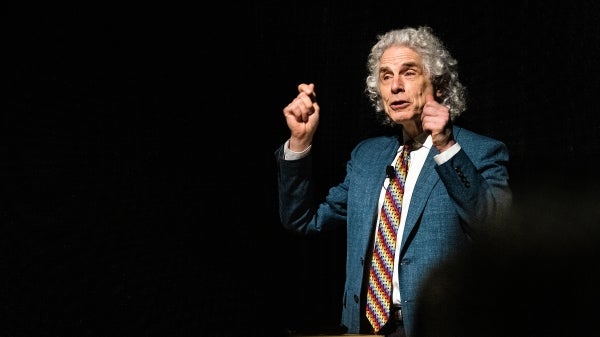
Popular science author Steven Pinker explores rationale behind irrational thinking at ASU event
Popular science author Steven Pinker returned to Arizona State University’s Tempe campus on Feb. 7 for a rational talk about irrational thinking.More than 200 people filled Marston Exploration…

Professor's expertise in DNA nanotechnology leads to top faculty honor
Arizona State University Professor Hao Yan works at the cutting edge of DNA nanotechnology, designing molecular building blocks to create complex systems.“I consider myself a biomolecular designer, a…